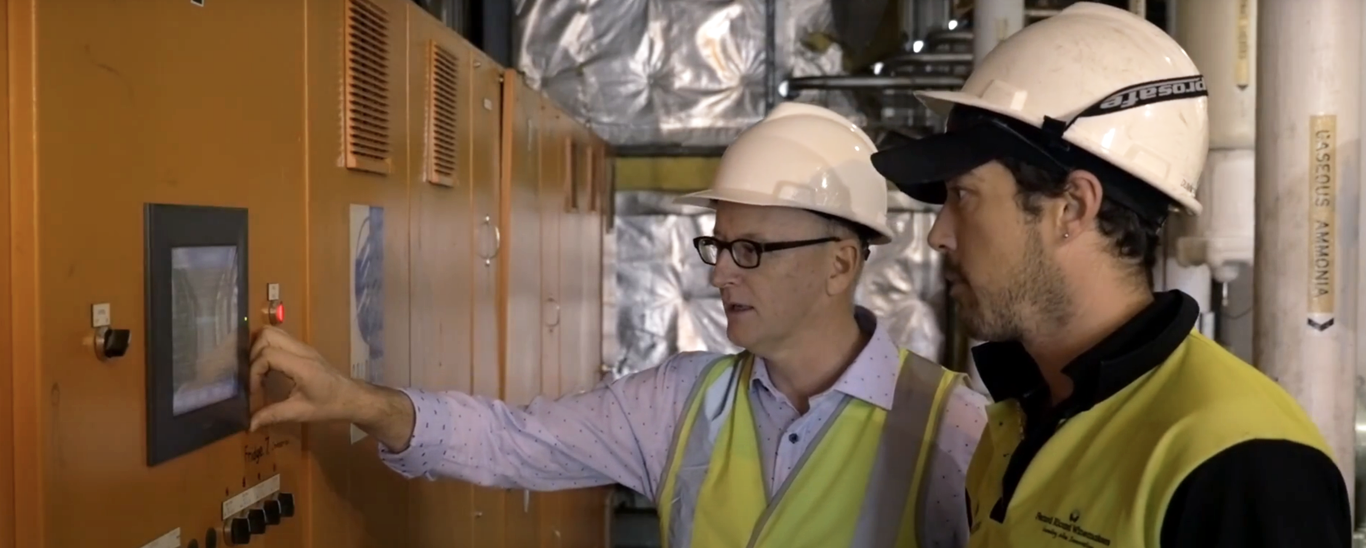
Targeted projects bring big energy savings
Jacob’s Creek is a leading Australian wine brand globally and one of the most awarded; but its environmental credentials are also impressive. Pernod Ricard Winemakers, which produces Jacob’s Creek and other brands at its Rowland Flat and Richmond Grove wineries in the Barossa Valley, has a long-term commitment to sustainable production and to green thinking across the production chain. There is a particular focus on reducing energy consumption and CO2 emissions, and a suite of recent projects has seen those emissions fall by more than 8300 tonnes per year. “A number of years ago the company embarked on a lean journey and recognised that the identification and removal of waste, in this case energy/ CO2, is not just good for the environment it is also good business,” said Global Operations Director Brett McKinnon. “These projects were identified as leading examples of where the business could reduce its consumption of energy and the subsequent impact on the environment.”
Pernod Ricard Winemakers has set itself ambitious targets to reduce energy use by 20% and CO2 emissions by 30% during the current decade and this is driving initiatives that are cascaded to every part of the business. “This is a very important signal of the commitment of the company and to the support required to fund and implement projects,” Brett said. The recent projects were diverse, ranging from adopting better wastewater aeration technology and fast-lift doors in cold-store warehouses to installing solar panels and LED lighting.
The results are impressive.
In the first 17 months after the load from two refrigeration plants was consolidated, for example, 1250 MWhr of electricity and 900 tonnes of CO2 were saved. Using new direct-drive harvesters reduced diesel consumption during the 2015 harvest by 30%, and using light weight bottles for six million cases of wine reduced CO2 emissions by 7600 tonnes, even before transport was taken into account. Changes to the winemaking process were also made. Moving to bulk fermentation of sparkling wine has saved energy from glass production, transport, storage refrigeration and wine processing. A significant capital investment was required to construct additional 5 mm thick pressure vessels to carry out the same process.
The key to success was undertaking a rigorous investigation of each individual project to quantify the potential benefits then monitoring progress post-implementation to ensure they were embedded into business practices and benefits were being realised. “In addition to these projects a number of focused projects have been carried out to develop systems planning and optimisation tools which have been implemented to improve the overall efficiency of operations,” Brett said. “This improved efficiency and has environmental spin off through savings in electricity and fuel”.